What Are Safety Standards For OEM Rack Batteries?
OEM rack batteries must comply with UL 1973, IEC 62619, and UN 38.3 certifications for fire resistance, thermal stability, and transportation safety. Critical features include IP55-rated enclosures, BMS fault detection, and cell-level fusing. Operating temperatures should stay within -20°C to 50°C (-4°F to 122°F).
What Determines Telecom Battery Dimensions in Network Infrastructure?
What certifications ensure OEM rack battery safety?
Key certifications include UL 1973 for stationary storage, IEC 62619 for industrial applications, and UN 38.3 for transport. These validate explosion prevention, overcharge protection, and vibration resistance.
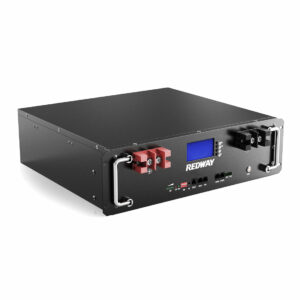
Beyond basic compliance, OEM rack batteries require rigorous third-party testing. The UL 1973 standard mandates 1.5x rated current overload tests for 10 minutes, while IEC 62619 requires 500-cycle lifespan validation under 45°C environments. Why does this matter? Imagine a subway system’s backup power: batteries must handle emergency loads without catastrophic failure. Pro Tip: Always request certification test reports – some manufacturers self-certify without independent verification. For hazardous environments, ATEX Zone 2 compliance adds explosive atmosphere protection, similar to offshore oil rig battery systems.
Standard | Focus Area | Test Duration |
---|---|---|
UL 1973 | Fire containment | 7-day thermal runaway |
IEC 62619 | Cycle life | 500 cycles @ 1C |
How do thermal management systems prevent failures?
Active cooling (liquid/forced air) maintains cells within 5°C differential, while NTC sensors trigger shutdowns at 65°C (149°F). Passive designs rely on phase-change materials.
Thermal runaway accounts for 78% of lithium battery failures per NFPA. Modern racks integrate multi-layer protection: ceramic separators melt at 135°C to block ion flow, while vented cell designs redirect gas away from adjacent modules. Think of it like a building’s sprinkler system – localized heat triggers targeted countermeasures. But what happens if cooling fails? Redundant dual-speed fans or glycol loops provide backup. Transitionally, battery enclosures now use aerogel insulation (NASA-grade) for 50% better heat retention than fiberglass.
Method | Cost | Max Temp Reduction |
---|---|---|
Liquid Cooling | $$$ | 20°C |
Forced Air | $$ | 12°C |
What BMS features are mandatory for OEM racks?
ISO 6469-1 requires voltage balancing (±30mV), SOC accuracy (±3%), and ground fault detection (<50ms response). CAN bus communication enables real-time diagnostics.
A BMS isn’t just a watchdog – it’s the battery’s central nervous system. Tier-1 systems monitor 16 parameters per cell, including impedance growth and anode potential. For perspective, data center racks need MTBF >100,000 hours on BMS components. Practically speaking, galvanic isolation between modules prevents cascade failures, much like submarine bulkheads. Two rhetorical questions arise: How often should BMS firmware update? Annually, to patch logic flaws. Can BMS units share data? Yes, via Modbus TCP integration with SCADA systems.
What mechanical safeguards prevent rack collapse?
19-inch racks require 1500lb vertical load ratings, 9.8kN seismic reinforcements, and 304 stainless steel frames. Anti-vibration mounts absorb 5-500Hz shocks.
Data center racks face unique stresses – a fully loaded 42U cabinet weighs over 2500lbs. Engineers use finite element analysis (FEA) to simulate rack deformation under earthquake loads (Zone 4 standards). Picture a skyscraper’s sway management: battery racks employ shear walls and cross-bracing to limit lateral movement to <3mm. Transitionally, epoxy-coated fasteners resist corrosion in 95% RH environments. Pro Tip: Deploy load monitoring strain gauges – they detect frame fatigue before visible cracks appear.
How do transportation standards impact rack design?
UN 38.3 mandates 2m drop tests, altitude simulation (15kPa), and vibration resistance (3.13G RMS). Stackable designs limit height to 2.2m for container shipping.
Shipping lithium racks involves navigating a regulatory minefield. Cells must survive 8-hour -40°C freezer tests (simulating cargo planes) and 250h salt spray exposure (marine transport). It’s akin to designing Mars rovers – batteries endure extreme conditions without maintenance. Notably, stack pressure control during transit prevents delamination – some OEMs use hydraulic dampers to maintain <10kPa inter-cell pressure. Transitionally, RFID tags now track shock events exceeding 5G during logistics.
What installation practices maximize rack safety?
NEC 480.13 requires 10mm inter-module spacing, copper busbars (500A/in² rating), and IR-camera inspections post-install. Concrete bases must absorb 2x rack weight.
Improper installation voids even the best OEM warranties. Teams should torque terminals to 12-15Nm using calibrated tools – under-tightening increases resistance by 200%. Consider a concert stage’s truss system: racks need load-path continuity from floor anchors to top panels. Transitionally, laser alignment tools ensure modules sit within 0.5° of vertical. Pro Tip: Perform dielectric strength tests (3000VAC for 1 minute) between racks and grounding points.
FAQs
Can OEM racks be retrofitted with third-party batteries?
No – vendor-locked BMS protocols often cause compatibility issues. Use OEM-approved cells to maintain warranty.
How often should rack grounding be tested?
Test ground impedance biannually – values over 0.1Ω indicate corrosion or loose lugs.
What Powers Cell Towers During Outages? Telecom Battery Essentials
Add a review
Your email address will not be published. Required fields are marked *
You must be logged in to post a comment.