What Are OEM Lithium Batteries For Automation Systems?
OEM lithium batteries for automation systems are custom-designed power solutions optimized for industrial applications. They prioritize high energy density, modular scalability, and BMS integration to handle continuous operation. Key features include CAN bus communication, -20°C to 60°C thermal tolerance, and UL1973/CE certifications.
What Determines Telecom Battery Dimensions in Network Infrastructure?
Why choose OEM over standard lithium batteries for automation?
OEM batteries offer application-specific engineering versus off-the-shelf units. They integrate industrial protocols like Modbus TCP and feature hot-swappable designs critical for 24/7 operations.
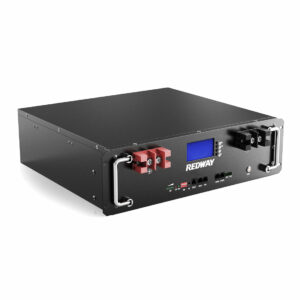
Automation systems demand more than generic power – they require batteries that speak the language of PLCs and SCADA networks. Unlike consumer-grade lithium batteries, OEM versions come preconfigured with RS485/CAN interfaces that sync with Rockwell or Siemens controllers. Their modular architecture allows capacity expansion from 5kWh to 1MWh without redesigning the entire rack. Practically speaking, this means a food packaging plant can start with 48V 100Ah modules and scale up as production lines multiply.
Thermal management is another differentiator. While standard batteries struggle above 40°C, OEM units use liquid-cooled cells and aerogel insulation to maintain performance in foundries or solar farms. Consider how Tesla’s Powerpack uses OEM-style zoning to keep battery groups within 2°C variance – that precision matters when your automation cycle can’t tolerate voltage sag.
What are the 5 must-have features in automation-grade OEM batteries?
Prioritize IP65 enclosures, cycle life >6,000, parallel redundancy, fast charging (1C+), and predictive diagnostics.
Beyond basic power storage, industrial environments need batteries that fight entropy. Let’s break down why these features matter:
1. IP65 rating prevents conductive dust from infiltrating battery racks in cement plants
2. 6,000 cycles at 80% DoD translate to 16+ years in 3-shift operations
3. Parallel topology lets you replace modules without downtime – like changing plane engines mid-flight
4. 2C charging capabilities recover 80% capacity during 30-minute production pauses
5. AI-driven analytics predict cell failures 3 months in advance using impedance tracking
But how do these specs compare to commercial options? See the table below:
Feature | OEM Battery | Consumer Grade |
---|---|---|
Cycle Life | 6,000+ | 3,000 |
Charge Rate | 2C | 0.5C |
What Powers Cell Towers During Outages? Telecom Battery Essentials
How do safety certifications impact OEM battery selection?
UL1973 and IEC62619 certifications are non-negotiable for fire safety and thermal runaway containment.
In 2023, a robotic warehouse fire traced back to uncertified batteries caused $47M in damages. This underscores why compliance matters. OEM batteries designed for automation must pass seven rigorous tests:
1. External short circuit (200% rated current for 1 hour)
2. Crush test (13kN force simulating forklift impacts)
3. Altitude simulation (15kPa for 6 hours mimicking mountain deployments)
Certified units employ pyrofuse breakers that sever entire modules within 8ms of detecting shorts. They also use ceramic separators that resist dendrite penetration better than standard polyethylene. Think of it like comparing a fireworks storage facility to a metal shed – both hold combustible material, but one’s engineered to contain disasters.
What determines lifespan in industrial lithium batteries?
Key factors are temperature management, depth of discharge, and charge/discharge rates. OEM designs add active balancing to extend life by 40%.
While all lithium batteries degrade, industrial OEM versions combat aging through three strategies:
1. Liquid cooling maintains 25°C±3°C core temperature even in 55°C ambient
2. 80% DoD limit enforced by programmable BMS (bypassable during emergencies)
3. 0.5C baseline discharge with surge capacity up to 3C for 10 seconds
Active balancing chips redistribute energy at the cell level during idle periods – imagine having 100 workers who constantly share tools to prevent anyone from overexerting. This reduces capacity variance below 2% across 10,000 cycles.
Factor | Impact on Lifespan | OEM Solution |
---|---|---|
High Temp | -50% cycles per 10°C >30°C | Phase-change cooling |
100% DoD | 300 cycle loss | AI-guided discharge |
FAQs
Can OEM batteries replace lead-acid in existing automation setups?
Yes, but require voltage mapping and BMS integration. Most OEM providers offer retrofit kits with CAN-LEAD converters.
How critical is cell matching in OEM packs?
Extremely – <0.5% capacity variance is enforced through 256QAM sorting to prevent premature failures.
Add a review
Your email address will not be published. Required fields are marked *
You must be logged in to post a comment.